Rotating Disk vs Fluidized Bed Thermal Spray Powder Feeders, which is better?
Rotating Disk Powder Feeder
When it comes to thermal spray powder feeders, a common question that comes up is: “What is the difference between a rotating disk powder feeder and a fluidized bed powder feeder?” An additional common question is: “Which is better?”
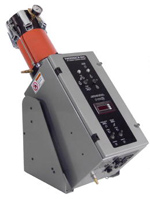
AT 1200
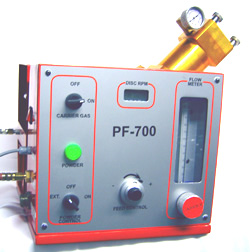
PF 700
The rotating disk powder feeder is a name that is rather self-explanatory of how it operates. The main operating component to feed the powder is a rotating disk. The AT 1200 and the PF 700 are both examples of rotating disk powder feeders. The rotating disk has a large number of small holes or slots that rotate in a circle. The hole rotates underneath the hopper that holds the powder. Gravity simply feeds the powder into the hole as it rotates past the powder discharge tube of the powder hopper. It rotates to another discharge hole where the powder drops down into the carrier hose where it is taken to the gun via the powder carrier gas. Some say this type of powder feed arrangement lends itself to the pulsating of the powder because of the interrupted flow. Others defend it saying that the length of the powder feed hose and the speed of the rotating disc eliminate the pulsation.
The rotating disk powder feeder is simple in design, reliable, and very easy to maintain. The man wear parts are the metal rotating disk, the plastic disk seal, felt seal, and various o-rings. With regular cleaning and preventative maintenance, the rotating disk powder feeders have proven to be reliable for many years.
Fluidized Bed Powder Feeder
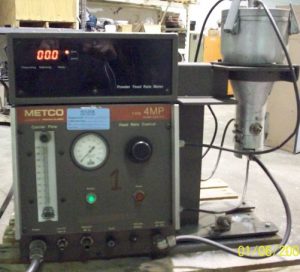
4MP Fluidized Bed Powder Feeder
The fluidized bed design is a little more complicated and needs more explanation. First, let’s start with the definition of a fluidized bed:
“A fluidized bed is formed when a quantity of a solid particulate substance (usually present in a holding vessel) is placed under appropriate conditions to cause the solid/fluid mixture to behave as a fluid This is usually achieved by the introduction of pressurized fluid through the particulate medium. This results in the medium then having many properties and characteristics of normal fluids; such as the ability to free-flow under gravity, or to be pumped using fluid type technologies. The resulting phenomenon is called fluidization.”
From Wikipedia, the free encyclopedia
The fluidized bed powder feeder design utilizes a portion of the carrier gas that is directed to the bottom of the powder hopper. This back pressure allows the powder to be “fluidized” with the carrier gas. In theory, this allows a more even size distribution and flow of the powder as it is drawn up into the powder pickup shaft. The powder pick up shaft has a converging/diverging internal design that creates a lower pressure inside the pickup shaft (Bernoulli principle) that draws the powder into the carrier gas stream and delivers it to the gun. Some say this creates a more continuous feeding of powder with less pulsation.
Even though these powder feeders have a vast array of hoses and pinch valves internally; when properly maintained they are reliable and remain workhorses in many coating shops. The complexity of the plumbing circuit is what draws the most criticism of this style powder feeder.
You will find plenty of opinions as to which is the better powder feeder; both the rotating disk and the fluidized bed powder feeders have been used successfully for many years in the thermal spray industry. I do have to say, the largest single problem I see with any powder feeder is the lack of preventative maintenance. Metal powders are abrasive and aggressive requiring regular cleaning and maintenance.
Click here to see more features of our new powder feeders: Powder Feeder Info