The Powder Flame Spray Process
The Powder Flame Spray process is also know as the Combustion Powder process. This is also called a Thermal Spray process. The operator injects a metallic or a non metallic into a combustion flame. The powder melts, atomizes, and sprays onto the surface being coated.
When an operator uses a Powder Flame Spray process, he mixes a combustable gas and oxygen together. Typical combustible gases are acetylene, propane, propylene, hydrogen, and natural gas. Some operators use standard compressed air instead of pure oxygen. It is more common to use bottled or liquid oxygen. The use of pure oxygen produces a hotter flame temperature that results in faster melting of the powder.
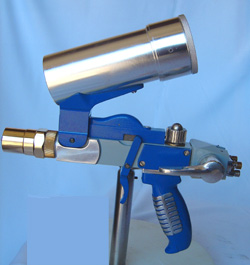
Powder Flame Spray Torch
In addition to the torch, an operator will use regulators, flow meters, and back flash arrestors to fully control the process. Controlling the variables gives a more consistent and higher quality coating.
The Powder Flame Spray process systems are relatively simple to use. Additionally they are relatively low cost to operate. It is common for machine shops operators to use them for the repair of damaged components. A common application is the need to repair a shaft that has a worn bearing seal area or a damaged shaft from a spun bearing.
The damaged component requires a machine operation to undersize, grit blast, and then spray with a material to make it oversize. Then a machining or grinding operation to restore it to the the originally size. Materials are available to customize the materials properties that are required for a specific application.
Typical applications for the Powder Flame Spray Process:
- Dimensional restoration
- Chemical attack resistance
- Wear resistance
- Gap clearance
- Abradable seal
- Spray and fuse