Thermal Spray Coatings
Thermal spray coatings are applied using a thermal spray torch to melt, atomize, and spray a metal, ceramic, or carbide onto a surface.
The thermal spray process is used to apply coatings to various surfaces for various purposes that include:
- Corrosion protection
- Dimensionale restoration
- Thermal conductivity
- Thermal insulation
- Wear resistance
- Chemical resistance
- Hard Chrome replacement
- Traction
- Lubricity
- Decorative
- Medical (bone growth enhancement)
In order to apply a thermal spray coating, you need the following basics for the process:
- Energy to melt the feedstock, typically from one of these sources;
- Electric
- Combustion Gases
- Plasma
- Velocity
- Feedstock
- Wire
- Powder
- Atomization gas
The feedstock is melted and atomized and applied in a way that is similar to applying spray paint. The major difference is that we are spraying molten metal, ceramic, or carbide, not an organic paint. We typically apply it in layers anywhere from .0005″ to .003″ thick, depending on the process and the material being sprayed.
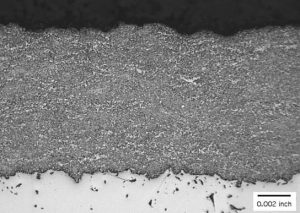
Thermal Spray Coatings
The above picture is a HVAF coating that is a 86% Tungsten Carbide, 10% Cobalt, and 4% Chrome.
The common processes are:
- Combustion wire (Also called Flame Spray Wire)
- Combustion powder (also called Flame Spray Powder)
- Twin wire electric arc
- HVOF, high velocity oxygen fuel
- HVAF, high velocity air fuel
- Plasma
- Cold spray
To compare these processes, please go to this link:
Thermal Spray Coating System Comparisons
Please explore the rest of this site to see more detail on each of the above items.